CBC CylinderBoreCoating
A future technology from HELLER
In 2011, Daimler AG and HELLER began a cooperation to jointly develop the coating process and get it ready for series production.
In 2013, HELLER and Daimler received the German Innovation Award for Climate and Environment in the "Process innovations for climate protection" category.
In 2016, the CBC technology was nominated for the German Future Award. At this time 32 machines had already been delivered to customers worldwide.
Since 2017, around a million four and six-cylinder engines have been produced using the CBC process every year at the Daimler Untertürkheim site alone.
In 2020, a total of over 100 systems for the coating of more than 10 million engines are in production worldwide.
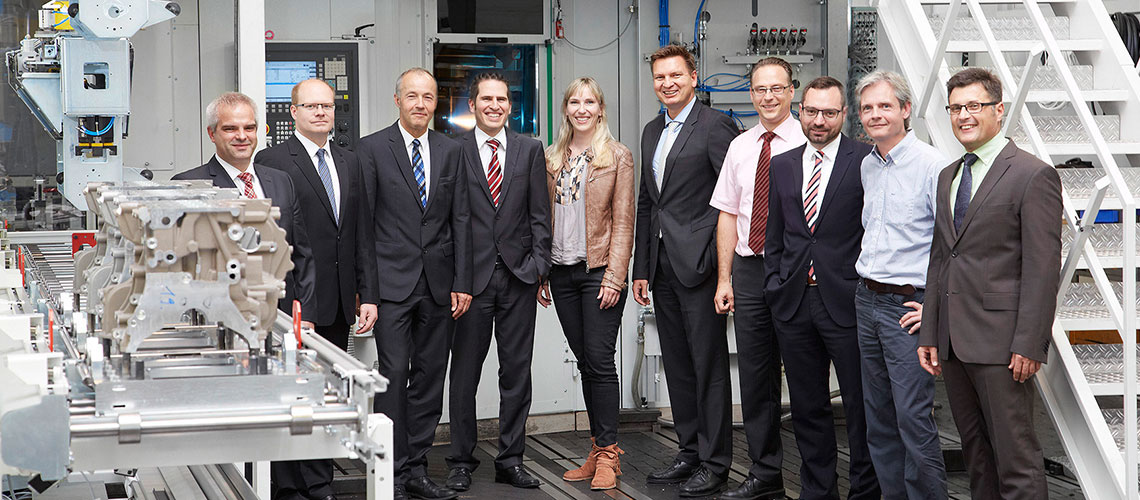
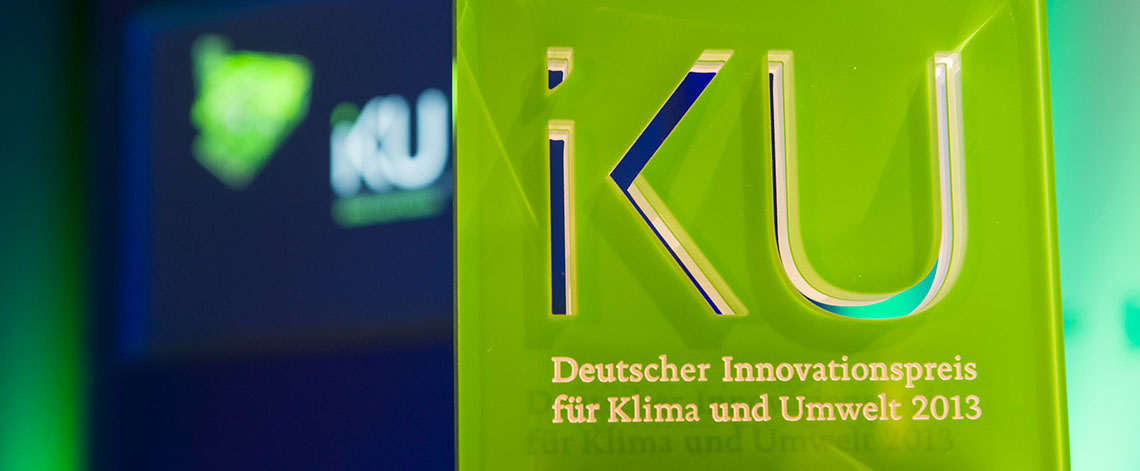
The CBC coating process
The mechanical foundation of the CBC coating process is the adequate preparation of the cylinder bore. A number of different roughing technologies are available for producing different surface conditions. To achieve the quality required for the coating process carried out in the second step, it is vital to create a structured surface quality whilst guaranteeing a precisely defined bore centre. To achieve this, HELLER decided to activate the surface using a machining process with a geometrically defined cutting edge to machine the cylinder bore to the required dimensions, whilst creating a precise helical roughened structure according to the requirements. Highprecision work in large-scale production. At the CBC TechnologyCenter in Nürtingen the roughing process is performed by an MC 20. The generated surface provides the pre-requisites for adhesive tensile strengths of up to 50 MPa.
Advantages of the roughening operation
- geometrically defined surface quality
- bore centre is defined by the machining centre
- adjustable roughening profile
- bore diameter and roughening profile are in a single operation
- flexibly adaptable process for various types of cast aluminium and cast iron
- precise and cost-efficient solution with a short machining time
Optionally, the engine block can be heated following the roughening operation. As a result, the bore diameter and the roughened structure are enlarged. This provides optimal conditions for step 2: the coating operation.
Currently, there are three different technologies available in the market for the coating of cylinder bores: the single-wire technology known as PTWA, the powder-based APS technology and twin-wire arc spraying or LDS. We have optimised the twin-wire process in terms of process and control technology, turning HELLER CBC into today’s leading coating technology for use in high-volume series production.
In the HELLER CBC 200 coating module a pair of steel wires, forming the anode and cathode, are melted by means of an electric arc. Using nitrogen as a process gas, the molten steel is applied onto the roughened cylinder bore structure in the form of droplets. This creates a 0.3 mm steel layer with the characteristic porosity the technology provides. The pores, which are adjustable in number and size, create the cavities for the oil retention volume and thus ensure the lubrication of the cylinder bore.
Advantages of coating using HELLER CBC
Robust process due to fully controlled process parameters:
- high deposition rate due to the use of two wires
- spray efficiency above 80 %
- continual layer build-up
- pores adjustable in terms of droplet size and number
Safe and efficient process:
- short coating time due to high deposition rate
- nitrogen as process gas is inexpensive and safe
- practically no oxides in the layer – ensures efficient fine machining
- powerful extraction system for a clean work environment
- no special wires required, but available on request
Guaranteed dimensional accuracy:
- low heat input into the workpiece due to low temperature of the molten particles
Prior to the final finishing operation, the CBC process comprises a finish boring operation. In this step, the precise shape and position of the cylinder bore are determined, creating the prerequisites for the honing operation. Contrary to alternative roughening and position honing processes offered in the market, the finish boring operation achieves the highest precision in terms of the layer thickness, whilst maintaining manufacturing tolerances.
Advantages of the finish boring process
- very short process time of approx. 12 sec. per bore
- highly precise cylinder geometries are created, whilst maintaining the geometric tolerances of the bores, resulting in an optimal utilisation of the friction advantages provided by the CBC coating process
- precise and cost-effective solution on standard machining centres
HELLER CBC 200 coating modules
Ready for large scale series production
- all process-relevant media are controlled
- automatic workpiece/adapter changer for shorter idle times
- automatic wire change with integrated wire cutting device and wire preparation during the coating process
- optimised access and easy to maintain torch unit
- global service availability
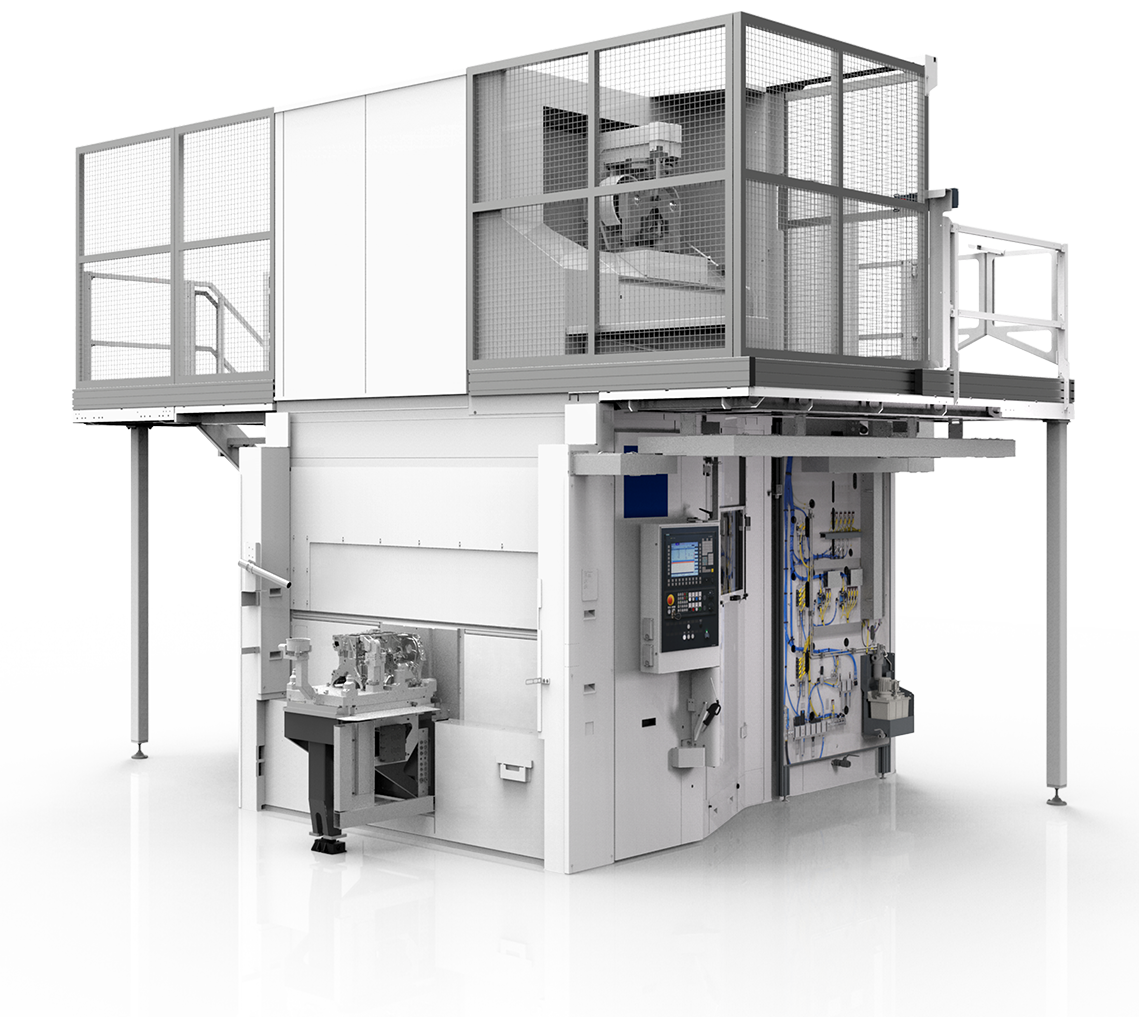
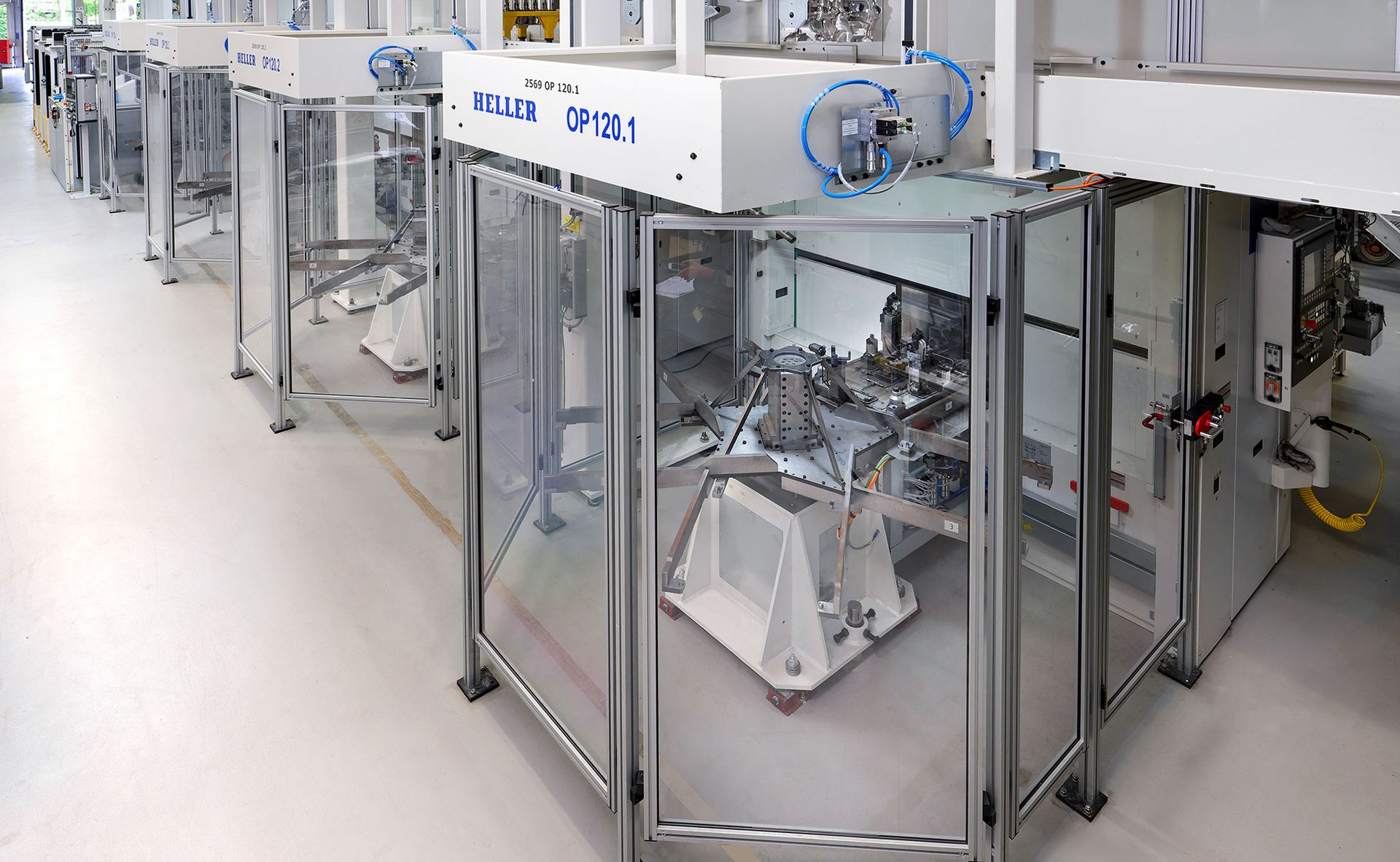
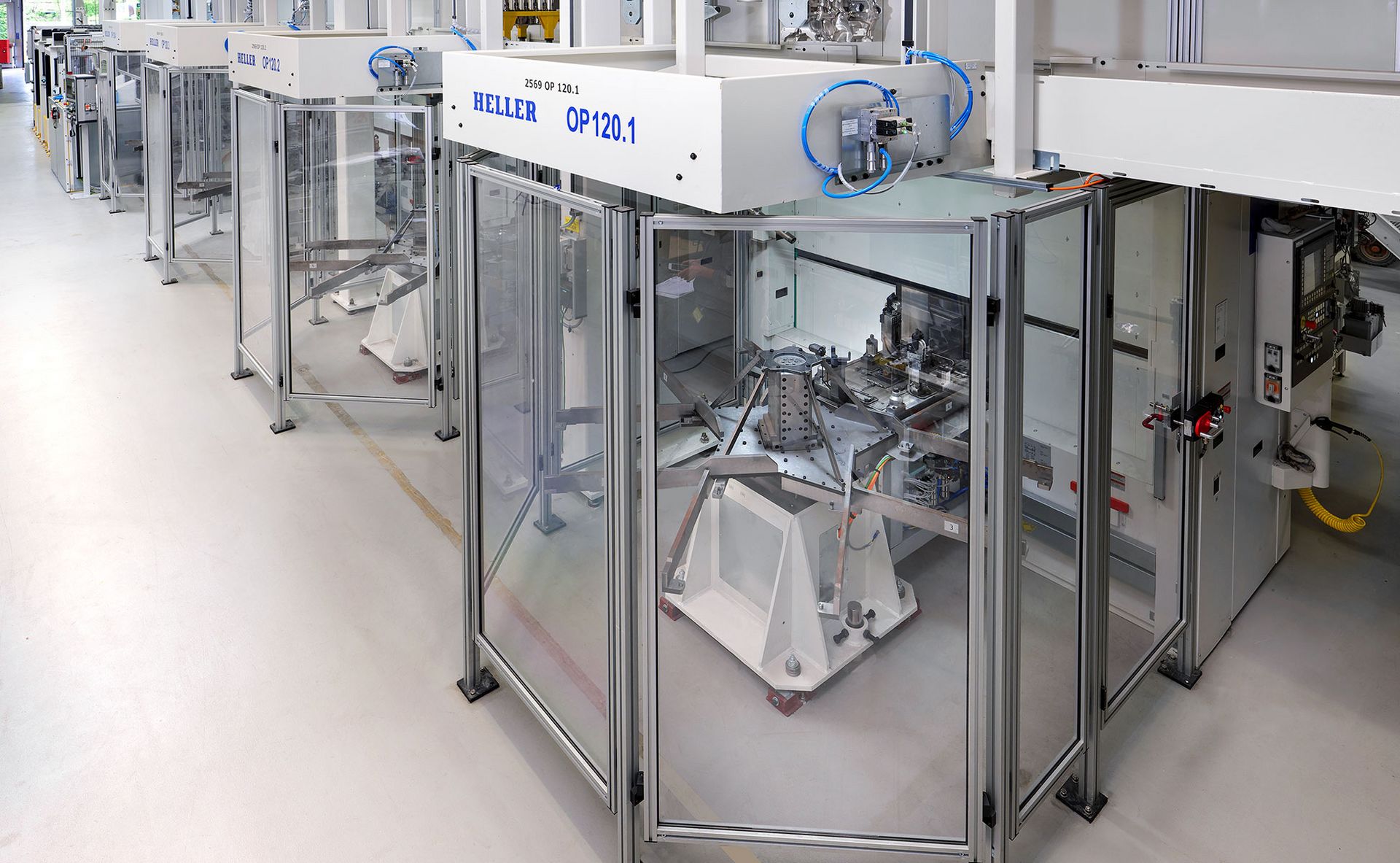
Technical data
Product selection | CBC 200 | |
Positioning range
X/Y/A | 750 mm / 610 mm / +/-47° | |
Clamping surface | 800 mm x 460 mm | |
Workpiece length | max. 600 mm | |
Clamping load | max. 150 kg (incl. fixture) | |
Acceleration
X/Z | 5 m/s² | |
Rapid traverse rate
X/Z | 40 m/min | |
Torch speed | max. 300 min⁻¹ | |
Coating time | ca. 30 sec per bore | |
Workpiece change time | ca. 20 sec | |
Torch and wire change time | ca. 180 sec | |
Engine types | I3 to V12 |
Downloads
At a glance, our Download Centre offers an extensive range of information materials about our company, our products and services for you to download.
Contact
Contact
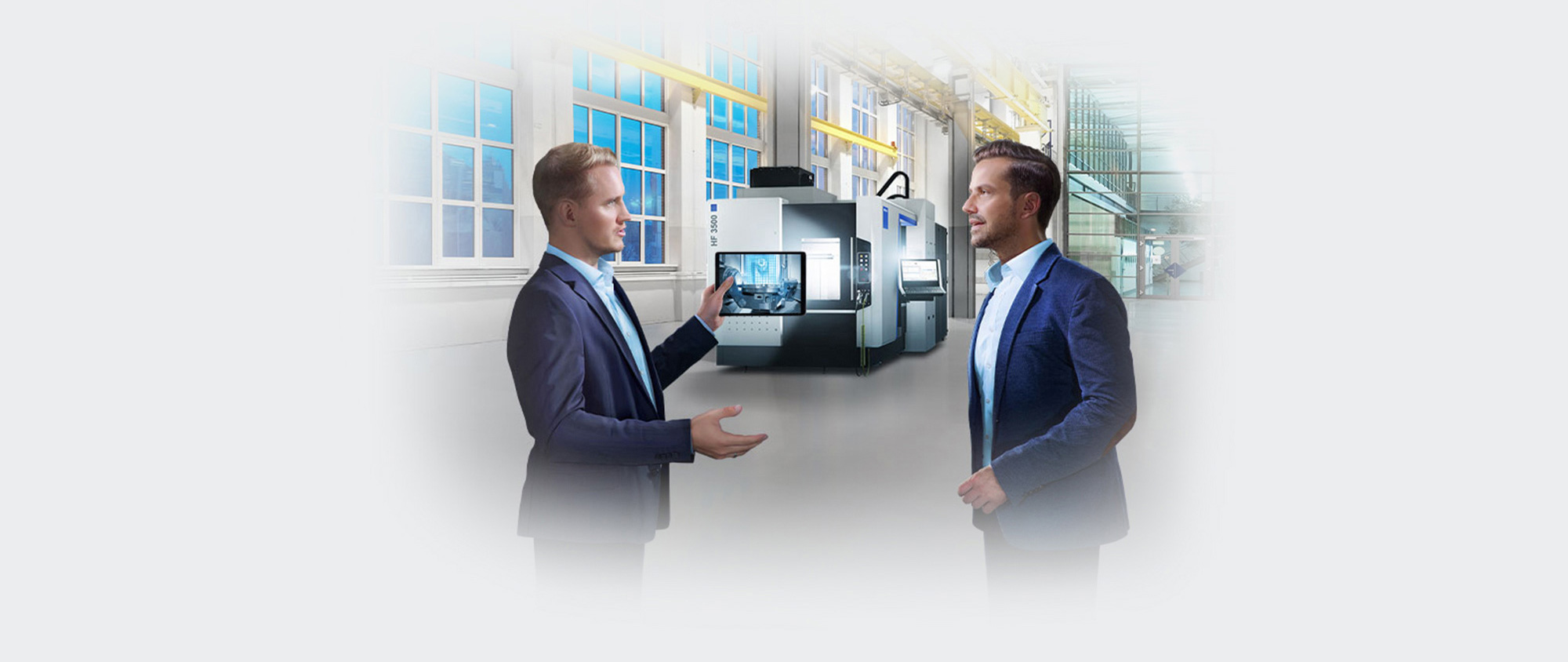
Sales & Services
Do you have questions about our products and services? Please get in touch with us, we are here for you! Benefit from our global HELLER network with knowledgeable sales and service contacts located in your region.
Find your nearest personal contact.
No results could be found.
You might also be interested in
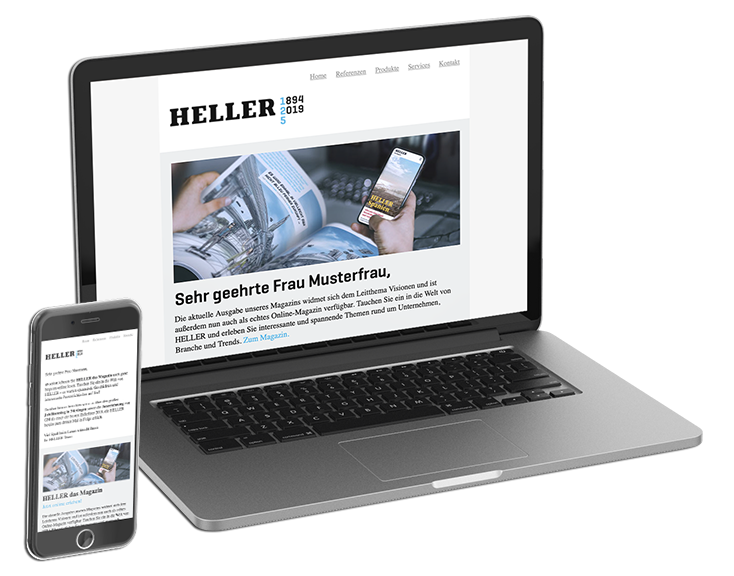
HELLER Newsletter
Register now!
The HELLER Newsletter provides you with information about all current topics concerning our company, our products and services as well as upcoming trade shows and events. Register now to make sure you never miss any news from the HELLER Group!